Barcelona-based IPE Industria Gráfica has invested in Fujifilm’s Activ LED curing system, as the Spanish label and packaging producer targets energy reduction as part of an ongoing sustainability drive.
IPE Industria Gráfica produces self-adhesive labels, sleeves, sachets and flexible packaging across a range of market sectors. Combining offset, screen, flexo and digital production methods, the company serves some of the biggest European and global brands.
Sustainability has long been a core focus of the business, leading the business to set up an eco-friendly portfolio of products five years ago. IPE Industria Gráfica also has FSC, PEFC and Carbon Footprint standard certification to underline its environmental credentials.
The company’s director general, Francesc Egea, sees UV LED curing taking this a step further and an important technology to make the whole industry more sustainable.
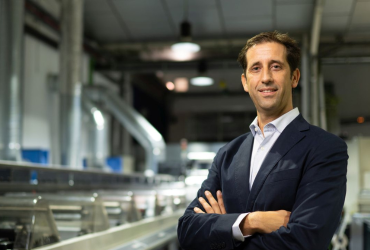
‘LED is the technology of the future,’ according to IPE director general Francesc Egea
‘LED is the technology of the future, there’s no doubt that this is the direction of travel,’ he commented.
‘At IPE, we’re market leaders and we’re prepared to take risks, especially when we see a technology that can help us to operate in a more sustainable way over the long-term. Fujifilm’s Activ UV LED curing system, with the huge energy saving potential it offers, is just such a technology.’
He continued, ‘We already had a very successful relationship with Fujifilm as a flexo ink supplier, so when we had some issues with our existing LED curing system and were looking for an alternative – it made sense on a number of levels to speak with Fujifilm.
‘Fujifilm is now a “whole solution” partner for us, giving us one point of contact for ink and for the curing technology if there are ever any issues.’
As well as the sustainability benefits, UV LED also brings to the business productivity benefits.
‘UV LED curing is the future, but not all LED systems are equal. We weren’t fully satisfied with our existing LED system, and in moving some of our sleeve and sachet production to Fujifilm’s Activ system we’re seeing a productivity increase of around 30%, as well as better quality finished products.
‘The level of continuous investment required to remain competitive in our industry is an ongoing challenge. But in Fujifilm we have a partner with both the ink and the curing solution to help us deliver better, faster results to our customers, while at the same time helping us to meet the ambitious sustainability goals we continually set for ourselves.’