A long and mixed history has given Edale a deep understanding of how to build the types of presses preferred by the narrow market today; modular, hybrid and bespoke. Michal Lodej went to visit the British press manufacturer to see how it is done.
‘We’ve got a year on Mark Andy,’ joked James Boughton, managing director of Edale. Although joking, he’s not wrong. Edale was started in December 1945 as an engineering company making bespoke machinery for the graphic arts industry. Under the name of Lonsdale, the company began to build its own design of stack label presses in the 1960s. In 1982 the company was bought by one of its distributors and became Edale, and then just five years later it was bought by the current chairman Grahame Barker in 1987.
Stack presses of course fell out of fashion and inline presses became the norm in the narrow web sector which Edale followed, leading it to eventually produce its first servo-driven press in 2000. The company then experienced success soon after by partnering with Agfa Graphics in 2002 to develop one of the earliest UV inkjet hybrid presses. Edale worked for 10 years alongside Agfa Graphics, which helped it move to a new facility in 2009, the place where the company is still headquartered today in
Whiteley, Hampshire.
Mr Boughton said, ‘The partnership with Agfa helped us to grow and allowed our investment into product development which has got us where we are today, in a position to work with the large multinational companies.’
Although the partnership with Agfa ended in 2012, it left the company in good stead with a deep understanding of constructing hybrid presses as well as the modular approach to press building which is a popular feature within the label sector.
Mr Boughton explained, ‘In narrow web printing, all machines vary in one way or another, you have to be able to change and modify your
machines if the customer needs something different.’
Streamlined production
To help streamline production the company is trying to standardise the print stations it builds and then modify them if needed at a later stage. This is part of Edale’s concept to build and put together a single print module to test it independently with out assembling the entire press, and is potentially two years away from turning that concept in a manufacturing reality.
Mr Boughton continued, ‘Even the most basic option of the new FL3 comes with all the configurations required for a modern label press as standard. We believe that in its standard form this press is more advanced than any other standard built press on the market, built with high quality parts, reasonable pricing, making it a high quality machine.’
This is the third generation of the FL3 press with the first being built in 2011. Edale has now begun standardising the web width of the press to 430mm and 510mm and according to the company, the newer model is more robust, more refined and designed with much more attention to detail with new cutting and finishing options.
Mr Boughton added, ‘We’re reducing the variation within our manufacturing, by making the highest specification print stations as standard. But by producing them in bulk we can keep costs down, so despite being a high specification unit, it will stay within our customers’ price range.’
The press comes with the company’s AiiR system which automates inking, impression and register settings on the press. Included as standard the press also sets up print to register marks, digital job sheet stores with the ability to recall all job setting parameters, and job sheet productivity rules.
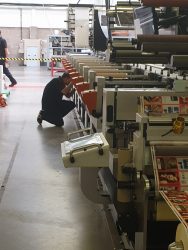
All Edale presses are built in the company’s factory in Hampshire
Comes as standard
The latest version of the FL3 is truly modular, to the extent that a single print station could be added or removed if required. Even in the instance of a mechanical failure at one station, the web could simply bypass the broken down unit and the machine would be able to continue printing.
One feature of the FL3 is that the inking system retracts from the print position while not in use, therefore depending on how many printing decks the press has; a printer can set up the next job while the press is running. This on the fly set up can improve productivity and help reduce downtime.
All Edale presses are shaftless and the FL series uses two servos and five stepper motors in each print station providing stable tension across the web and accurate registration. The presses also use a gearless impression system which avoids any gear mesh between the print cylinder and impression roll.
Due to its modular system and Edale’s experience with hybrid press manufacturing there is no surprise that hybrid versions of the press are available. For those who do not require the full digital outfit, Edale also offers its EFX Print Bar, a UV based inkjet system that can provide print finish or embellishment capabilities such as cold foil, high build varnish effects, high opacity whites or even single colour variable data.
Other options to add to the press include the EZ Die die-cutter changing system which allows the operator to remove the die cylinder out of the press without having to lift it from the machine. It simply slides out onto a trolley with the same process for putting the new cylinder back into the press in less than 60 seconds.
Carton work
While the FL3 is mainly aimed at narrow web printers, the company also manufactures a press dedicated to single pass carton printing, the larger FL5 series. What makes it aimed towards carton board is the fact it can run substrates up to 700microns at 570mm wide.
The FL5 is nearly always paired up with another machine in the company’s portfolio, the FDC, web-fed flatbed die-cutter. This machine can run inline with the FL5 and at speed up to 80-90m/min. The two together are tailored for short run high value carton work and is successfully being used by Bury-based printers Reelvision, which is a leading provider for cosmetics and pharmaceutical packaging.
The company’s facilities and expertise means it does not just construct its own machines but also builds units in collaboration with other industry suppliers, such as AGB’s Digicon 3000. The 760mm wide finishing machine runs inline with HP presses, 80% of them are currently converting film and it can work with all ink types.
Looking to what is in store for the future of the company, as with all British manufacturers, depends in some ways on Brexit and the way it is handled, however the company is already experiencing growth into the Indian market, and will continue to develop this.
Closer to home, the company will be exhibiting at Labelexpo Europe 2019, held in Brussels 24–27 September. This year it plans on using its modular capabilities to provide a more interactive experience for visitors to its stand, with what it has called a deconstructed flexo press.
The company will be displaying different print and die-cutting stations, standing individually giving customers the chance to get hands on with different parts of the press. Mr Boughton explained, ‘We wanted to do something different from the same old routine of running a press in front of a crowd kept behind a ribbon. We want to give visitors a chance to get to know the machine better and this way they can see for themselves how an anilox is changed, and how it feels to operate the press. Hopefully this way they will get to know the press, and Edale a little better.’